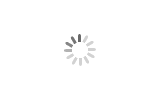
Custom, cost-effective machining solutions
• Precision CNC machining follow customer's requirements
• Complete CNC production, including precision CNC milling and turning
• Complex machining, assembly, weldments, and more
• Short run & Rapid lead times
• Contract manufacturing for prototypes & high volume order
Surface treatment is a process method to artificially form a surface layer on the surface of the substrate which has different mechanical, physical and chemical properties from the substrate. The purpose of surface treatment is to meet the corrosion resistance, wear resistance, decoration or other special functional requirements of the product. For the metal castings, our common surface treatment methods are mechanical polishing, chemical treatment, surface heat treatment, spraying surface, surface treatment is to clean the surface of the workpiece, cleaning, deburring, deoiling, deoxidizing skin.
Product Description
Common methods to prepare DLC films include vacuum evaporation, sputtering, plasma-assisted chemical vapor deposition and ion implantation and so on.
Of these methods, the traditional method of vacuum evaporation coating has high deposition rate, film generated high purity, but due to thermal evaporation of atoms or molecules in the substrate energy is very low (about 0 - 2 eV), its surface mobility is very low, lead to the film and substrate bonding strength is poor, and have deposited atoms to fly to cause the shadow effect, makes the application of vacuum evaporation coating technique was very limited. The ion implantation method can significantly change the friction factor, wear resistance and corrosion resistance of the material, and there is no clear interface between the injection layer and the matrix material, so it is firmly bound to the matrix, and there is no adhesion fracture or peeling on the surface. However, the implantation layer of ion implantation is too thin, only a few hundred nanometers, which limits its application in wear-resistant conditions.
In order to overcome the problems of poor adhesion of vacuum evaporation deposition method and shallow implantation layer of ion implantation method, researchers combined thin film evaporation deposition and ion implantation technology to develop vacuum evaporation ion beam assisted deposition technology [5, 6]. The technique involves bombarding the coating with ions while depositing elements on the substrate with an evaporation source (electron beam) to obtain a high performance dense film layer thicker than the ion implantation layer and more adhesion than the evaporation deposition method. Therefore, this method is beneficial to enhance the tribological properties of thin films. In this paper, the tribological properties of DLC films were tested by vacuum evaporative ion beam assisted deposition, and the effects of surface morphology of DLC films on tribological behaviors were studied.
Smooth and compact DLC films were formed on the surface of spring steel and T i6A l4V ball after vacuum evaporated ion beam assisted coating. Tribological test results showed that DLC films reduced the friction factor of matrix materials and improved tribological properties. SEM and AFM analysis of the worn surface showed that the surface wear of DLC film was lighter than that of bearing steel, showing slight wear traces, indicating that the tribological properties of spring steel matrix were significantly improved after being treated by vacuum evaporated ion beam assisted technology. AFM analysis also showed that after DLC film was plated on the surface of T i6A l4V ball, the surface of wear marks was smoother and smoother than the original surface before wear, with less surface roughness, and its tribological properties were further improved in the friction process.
Advantage:
1. Hexiang is specialized in doing OEM/ODM precise products according to customers drawings or samples
2. Software for specification drawings: Pro/E, Auto CAD, solid work 2001,CAXA,UG,CAD,CAM
3. Certificates: ISO 9001:2008
4. Fast delivery
5. 10-year machining experience, using high quality raw materials, 100% quality inspection before delivery
6. Advanced equipment, excellent R&D teams and strict quality control system
So, we can achieve Competitive price with good qualit, low MOQ and short lead time.